Sintered Silicon Carbide –SSiC
(常壓燒結碳化矽)
High Temperature and Corrosion Resistant, Produced at Low Cost
SSiC is formed by bonding together the crystals of alpha silicon carbide (α-SiC), which form at very high temperatures.
It’s hardness is second only to that of diamonds, and is highly resistant to granular abrasion. The high purity of our ceramics (>98% SiC) also means they can withstand contact with the acidic and alkaline substances that machine components come in contact with in the chemical industry.
They can also withstand temperatures as high as 1650°C and are resistant to the oxidization effects that typically occur at high temperatures with other materials.
It’s hardness is second only to that of diamonds, and is highly resistant to granular abrasion. The high purity of our ceramics (>98% SiC) also means they can withstand contact with the acidic and alkaline substances that machine components come in contact with in the chemical industry.
They can also withstand temperatures as high as 1650°C and are resistant to the oxidization effects that typically occur at high temperatures with other materials.
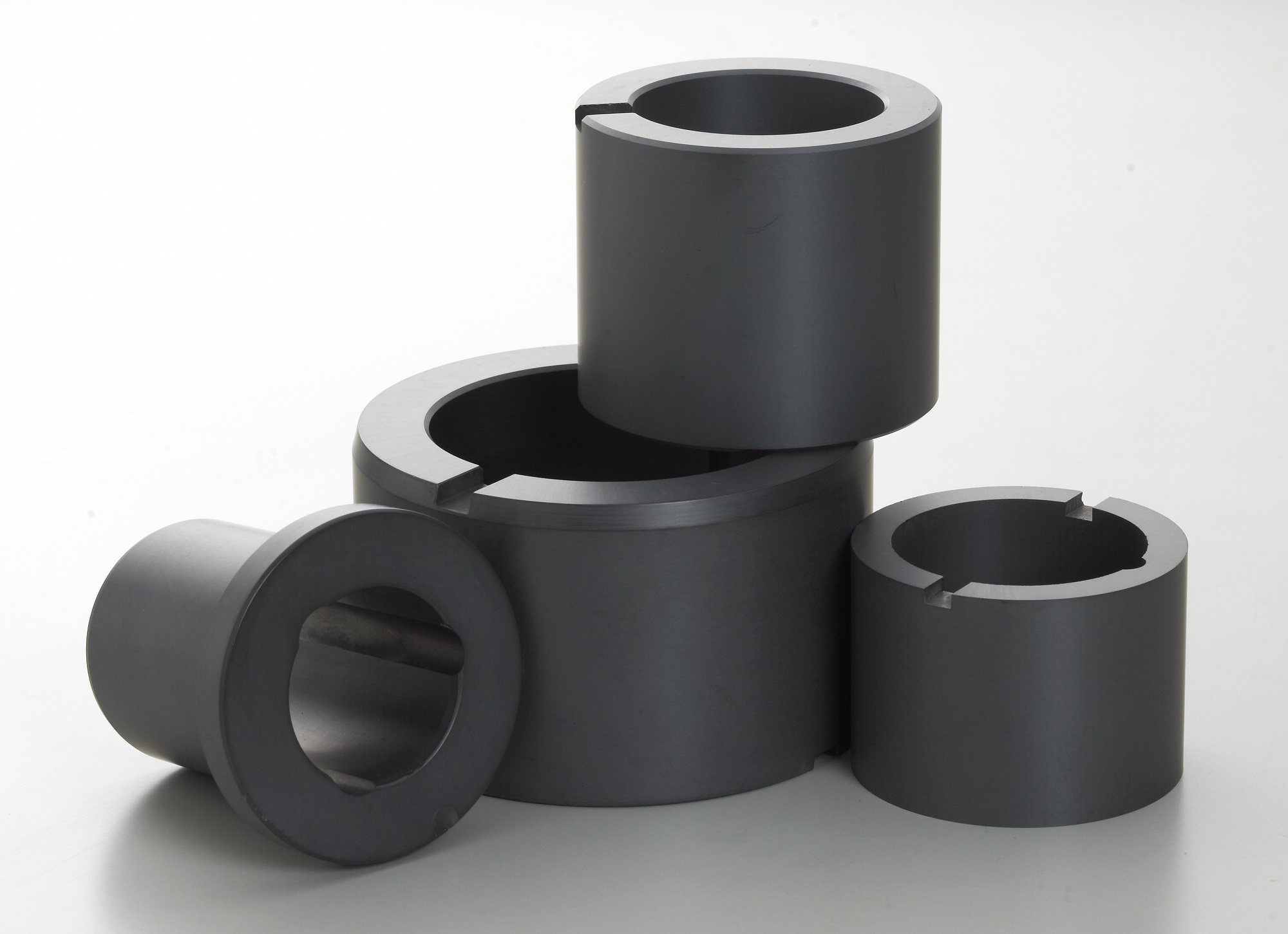
SSiC is one of our most important products. Its mechanical performance is close to that of high-pressure silicon carbide (HP-SiC), while its structural machinability is even higher than that of HP-SiC.
Its low cost means it is well-suited to mass production, while its high degree of machinability makes it suitable for complex designs. SSiC is particularly suitable for use in high-efficiency machine components such as glandless pumps and magnetic drive pumps, where other materials will rust or erode over time, or deform due to inadequate durability or resistance to heat.
The use of SSiC-based components reduces operational costs, as components do not require frequent replacement.
Its low cost means it is well-suited to mass production, while its high degree of machinability makes it suitable for complex designs. SSiC is particularly suitable for use in high-efficiency machine components such as glandless pumps and magnetic drive pumps, where other materials will rust or erode over time, or deform due to inadequate durability or resistance to heat.
The use of SSiC-based components reduces operational costs, as components do not require frequent replacement.
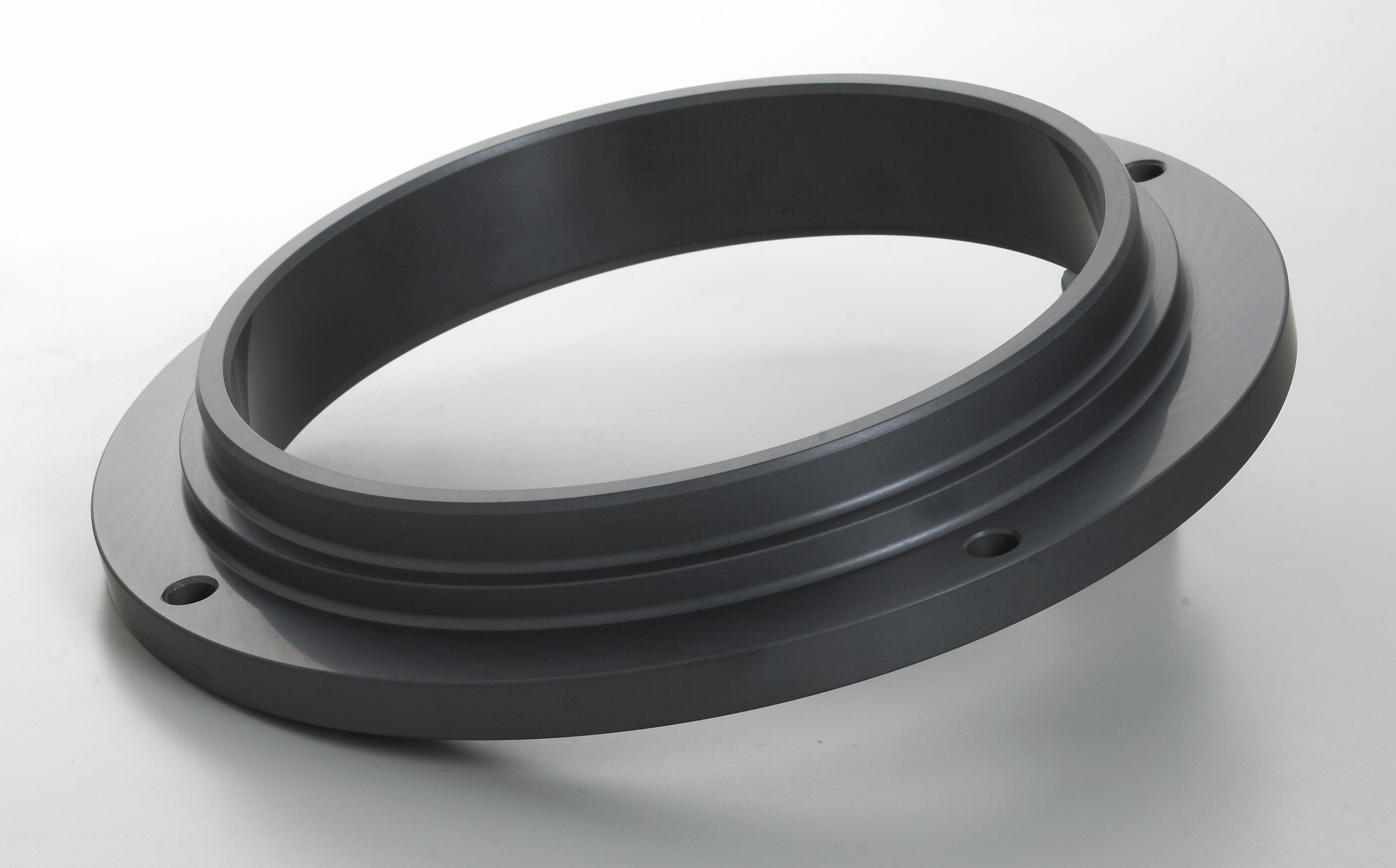
Sintered Silicon Carbide Related Data
Main component | 99%Al2O3 | S-SiC | ZrO2 | Si3N4 | TC | ||
. | |||||||
Physical Property | Density | g/cm3 | 3.90 | 3.1 | 6 | 3.2 | 14.55 |
Water Absorption | % | 0 | 0.1 | 0 | 0.1 | – | |
Sinter Temperature | °C | 1700 | 2200 | 1500 | 1800 | – | |
Mechanical Property | Rockwell Hardness | HV | 1700 | 2200 | 1300 | 1400 | – |
Bend Strength | kgf/mm2 | 3500 | 4000 | 9000 | 7000 | 7000 | |
Compression Intensity | Kgf/mm2 | 30000 | 20000 | 20000 | 23000 | 23000 | |
Thermal Property | Maximum working temperature | °C | 1500 | 1600 | 1300 | 1400 | 1400 |
thermal expansion coefficient 0-1000°C | /°C | 8.0*10-6 | 4.1*10-6(0-500°C) | 9.5*10-6 | 2.0*10-6(0-500°C) | 2.0*10-6(0-500°C) | |
5.2*10-6(500-1000°C) | 4.0*10-6(500-1000°C) | 4.0*10-6(500-1000°C) | |||||
Thermal Shock resistance | T(°C) | 200 | 250 | 300 | 400-500 | 400-500 | |
Thermal Conductivity | W/m.k(25°C | 31 | 100 | 3 | 25 | 25 | |
300°C) | 16 | 100 | 3 | 25 | 25 | ||
Electrical Property | Resisting rate of Volume | ◎.cm | |||||
20°C | >1012 | 106-108 | >1010 | >1011 | >1011 | ||
100°C | 1012-1013 | – | – | >1011 | >1011 | ||
300°C | >1012 | – | – | >1011 | >1011 | ||
Insulation Breakdown Intensity | KV/mm | 18 | semiconductor | 9 | 17.7 | 17.7 | |
Dielectric Constant (1 MHz) | (E) | 10 | – | 29 | 7 | 7 | |
Dielectric Dissipation | (tg o) | 0.4*10-3 | – | – | – | – |
Sintered Silicon Carbide Application Areas



Main Uses For Sintered Silicon Carbide (S-SiC)
Application Environment | Applications | Qualities | |
---|---|---|---|
Petrochemical | High Temperature High Hydraulic Pressure Abrasion |
Nozzles Mechanical Seals Bearings Ball Valves Valve Plates |
Wear Resistant |
Chemical | Strongly Acidic Strongly Alkaline High-Temperature Oxidization |
Mechanical Seals Bearings Pump Assemblies Heat Exchangers Ventilation Piping Thermocouple Sheaths |
Corrosion Resistant Wear Resistant Air Impermeability High Temperature Corrosion Resistant |
Mechanical | Engines Abrasion |
Nozzles Turbine Blades Rotors Combustion Device Components Sand-Blasting Nozzles Container Lining |
Thermal Shock Resistant Wear Resistant High Strength Wear Resistan |
General Industry | Pulp Mill Waste High Temperature High-Power Heat Dissipation |
Mechanical Seals Bearings Molding Plates Kiln Furniture Heat Transfer Materials Crucibles Encapsulationmaterial Substrates |
Corrosion Resistant Wear Resistant Heat Resistant Fast Heat Ttransfer High Thermal Conductivity |
Nuclear Power / Laser | High-Temperature Boric Acid High Power |
Mechanical Seals Axle Sleeves Reflection Screens |
Radiation Resistant High Strength Highly Stable |
Metallurgy | Heat Resistantmaterial Heat Exchangers |
Heat Resistant Corrosion Resistant Oxidation Resistant Air Impermeability |
CM Advanced Ceramics - Sintered Silicon Carbide Standard Production Process



As a specialized manufacturer with over 30 years invested in the research and development of applications for Sintered Silicon Carbide, Aluminium Oxide and Partially Stabilized Zirconia, CM Advanced Ceramics is able to produce a wide variety of precision ceramic products customized to our clients’ needs.
We employ a vertical integration approach to manufacturing, controlling all stages from material acquisition to production. Our manufacturing process adheres to ISO9001 standards and follows strict quality control procedures to ensure a long life cycle for all of our products. At the same time, we possess the ability to produce our own molds. This gives us great flexibility in mold design and allows us to quickly and accurately produce molds that meet our client’s needs, all while reducing production costs.
We happily share profits with our clients who can enjoy discounted quotes for the first order. In these ways we help open up new business opportunities for our clients who in turn can enjoy even greater profit. If you are looking for a NEW manufacturer, please contact with us RIGHT NOW.